Processes behind fabricated steel structure
Pre-fabrication processes
The first step is design preparation which is where the project’s drawings and specifications are created and agreed upon. Weldform Structures specialises in state-of-the-art steel 3D modelling where we use the latest Advanced Steel 3D modelling software to produce accurate and reliable drawings for your project.
Once the design is completed, a Bill of Material (BOM) and Bill of Operations (BOO) will be drafted to prepare the necessary information for purchase and production. After the BOM is created, the next step is material acquisition where the materials required for the project will be acquired from the steel supplier and will be delivered to the fabrication site.
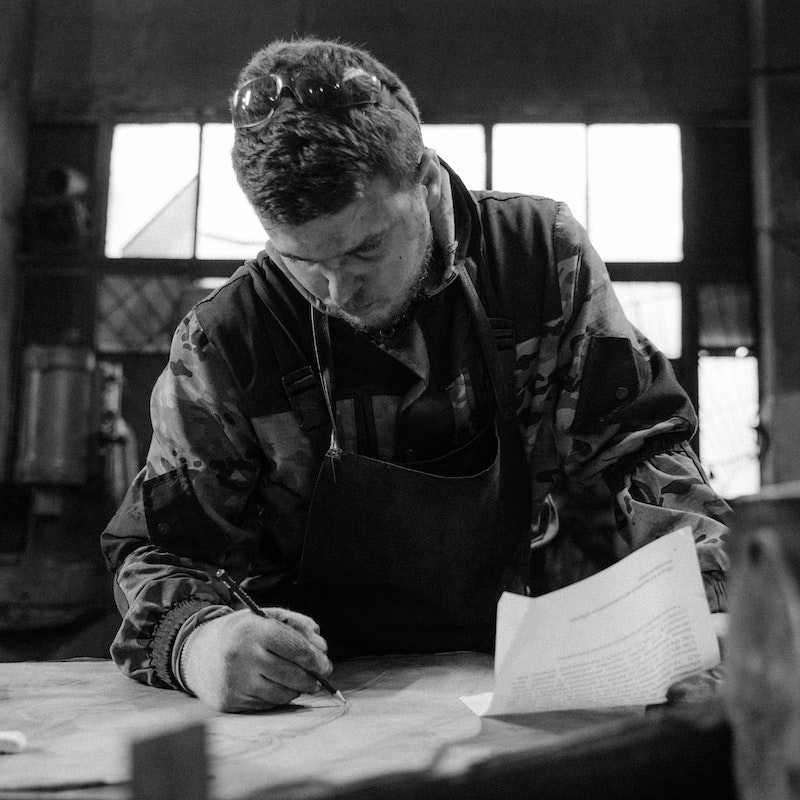
Core processes
After the preparatory processes, the fabrication process begins with steel cutting and drilling. Laser cutting machines, plasma torches, and computer numerically controlled (CNC) are used to cut high-grade steel by shearing, sawing or chiselling.
Once the steel is cut and drilled, the steel is then bent and welded to create the desired shape. Bending processes include section bending, roll bending, plate bending, and tube bending while welding can be performed by hand or a machine, using either MMA welding or MAG welding.
Post-fabrication processes
After the steel is fabricated, a quality check is conducted through visual inspections, dimensional inspections, and mechanical tests to ensure that the steel meets the required specifications. If required, non-destructive testing (NDT) is also performed to further inspect the welded steel and ensure that there are no hidden defects and cracks.
The process continues by turning the fabricated components into final steelwork ready to be supplied to the client. This includes surface preparation, corrosion protection (by painting or galvanising), and steelwork erection.
Finally, the steel is delivered to the site and assembled according to the design. The assembly process involves bolting and/or welding the steel parts. Installation of the steel parts must be handled carefully to avoid damage.
At Weldform Structures, we pride ourselves on having a highly skilled onset team of welders, dogmen, riggers, and crane operators for installation. We conduct careful planning prior to erection to reduce any risk of injury and additional financial costs.
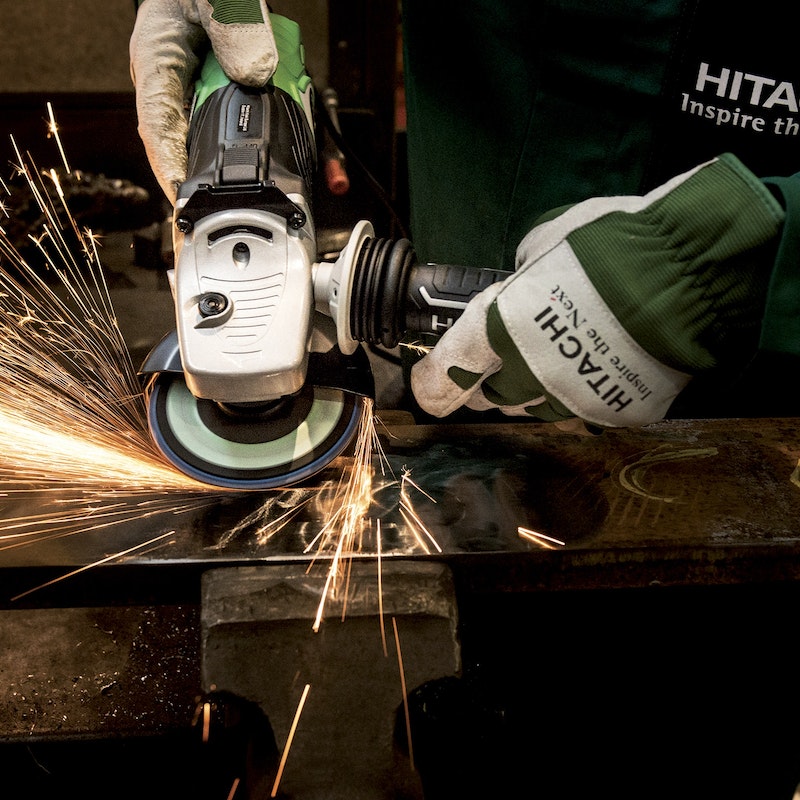
Technological innovation and trends in steel fabrication
Modern steelwork fabrication has computer-aided design and detailing (CAD) that is directly linked to the factory floor computer numerically controlled (CNC) machinery. This fosters a higher degree of accuracy in transmitting information which further increases the quality standards of production.
Overall, technology has played a pivotal role in advancing steel fabrication. Plasma cutting and robotic machinery enhance productivity whilst aiding in producing parts with higher accuracy and quality, providing significant benefits both to the client and the main contractor.
At Weldform Structures, we link our drawings, namely NC, DXF, and DSTV files to a 3D modelled structure where all changes and revisions can be automatically updated and managed. This way, we streamline the process of steel installation, preventing errors and saving time on site.
Choose Weldform Structures today
Weldform Structures is an expert in the field of structural steel. We are anchored in a commitment to deliver unwavering quality in all facets of our operations and production. From our extensive track record, we are committed to not only delivering construction projects of the highest calibre, but also leveraging cutting-edge technologies to ensure the most efficient, cost-effective, and timely outcomes for our clients.